Introduction:
Imagine playing pickleball confidently, winning points, and cheering yourself for top-notch gameplay. Every pickler wants a fair and smooth game with good-quality equipment. And, a paddle turns the cards for you to achieve victory. I started playing with a wooden paddle when I was a kid.
I used to practice my serves and shots for hours and hours on the pickleball court back then.The youngest brother of mine is a mechanical engineer and we always have thorough discussions, arguments about materials, manufacturing technology, processes and their impact on efficiency. These long discussions within our family have helped me to understand in depth.
I have probably tested and used all the paddles available in the market and also made many DIY paddles with my brother. You will find the wall gallery in my home where I have a collection of all the paddles starting from the very first till Today.I was intrigued with pro paddles, their features, and their ultimate performance. I still remember when I got my first professional carbon fiber JOOLA Perseus paddle, my happiness was at the top of the mountain! My best performance was when I competed in the Atlantic City Pickleball Open in September 2022. In this article, we will explore ‘How a paddle is made?’, in easy and simple ways.
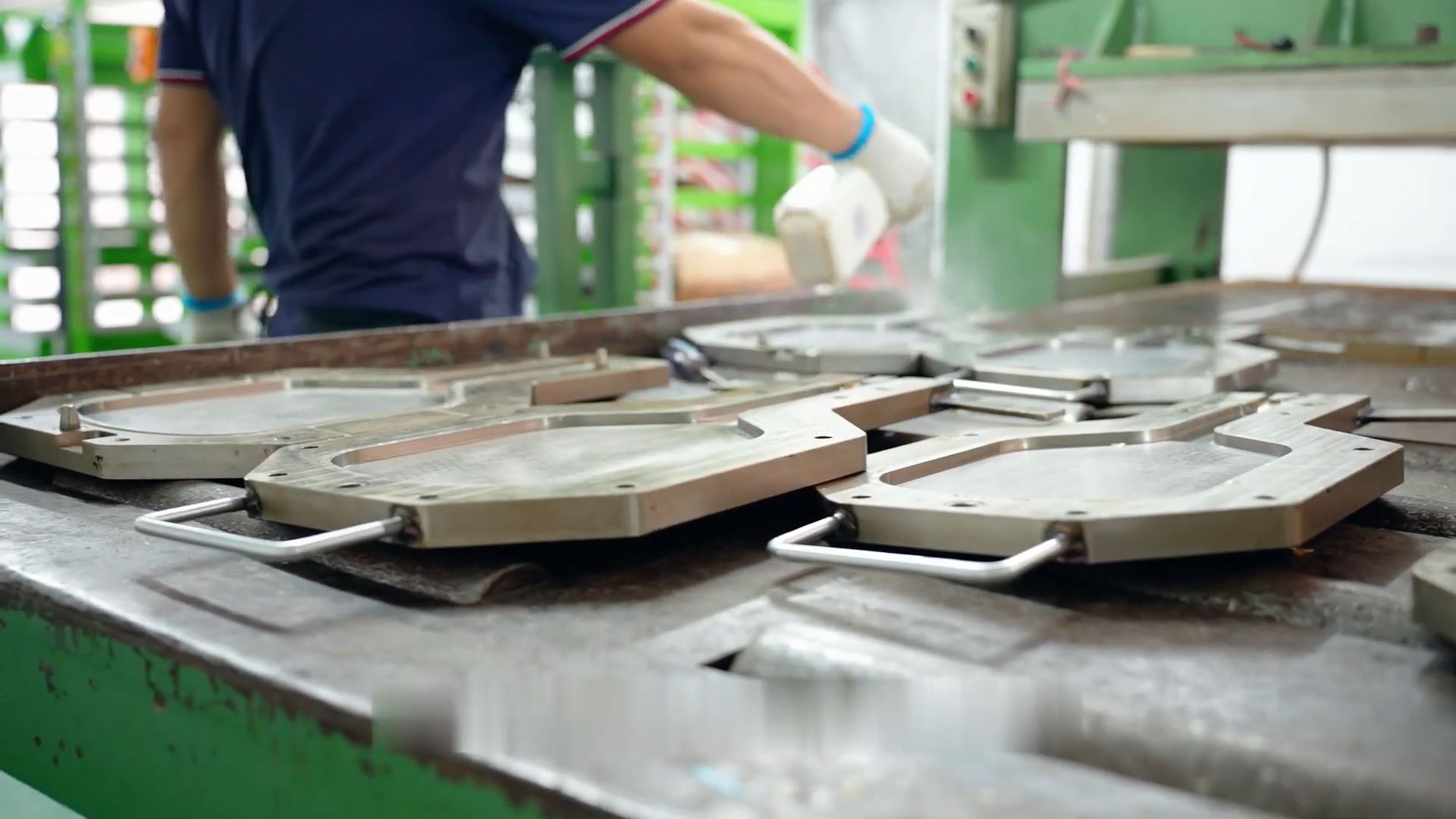
Source Url: https://www.youtube.com/watch?v=6UkD4VZ2y5w
What Was The First Pickleball Paddle Made Out Of?
In 1965, Joel Pritchard and Barney McCallum found their families getting bored on a sunny hot afternoon. They told their kids about finding a new game to pass the sweaty afternoon. That’s when the discovery of pickleball started. That didn’t last long, though, as they consistently broke during play. They used wooden ping pong paddles as the pickleball paddle to play for the first time.
Soon they realized that these wood paddles tend to break, have a large thickness, and are a bit heavier. Players had to add up extra power to serve the ball. They created another paddle from fabricated plywood. They kept their experiments on to find the perfect paddle. McCallum called these newly invented paddles ‘M2,’ which were famous back then among pickleball players.
How Is A Pickleball Paddle Made?
Those were nostalgic days when I started my pickleball journey. I used to experiment with different types of paddle starting with wood, later many paddles like the Onix Z5 and SLK graphite core paddle.I have experienced that with new materials and technology designs the power requirement to hit the ball is optimized.
My gameplay and performance transformed when I started playing with RCF- Raw carbon Fibre and thermoformed paddles. I started researching these revolutionary paddles.
Paddles are categorized as Generational 1, 1.5, 2, etc., based on the type of technology utilized to create them. I would like to share its manufacturing journey with you guys too, which is as follows;
-
Sandwich Method:
With accurate precision, the paddle manufacturers can add the top face sheet, middle honeycomb core, and bottom face sheet while forming a paddle.
The sandwiched core between the surfaces is the ‘paddle’s panel’. The panels on both sides are stuck to the top and bottom face with a strong adhesive glue. This process is also called the ‘cold-mold’ method because no heat is involved to form paddles. These glued faces are now colored with decided surface designs with micro-graphic printing machines. These faces appear smooth and leave a great spin for serves.
A safeguarding edge guard is added to the edges of this paddle to protect it from wear and tear. Such paddles are recognized as ‘Gen 1’ because of their conventional way of processing. Many Yonex paddles are created similarly with proper sandwiching and gluing with a suitable edge guard. They have a wooden grip which is later covered with a rubber film in an aligned direction for firm handling.
-
Carbon Fiber Weaving Method:
The ‘Raw carbon fiber’ (RCF) is the foundation behind making these carbon fiber weaved Gen 1 paddles. The ’ Electrum Model E’ is the first Gen 1 RCF technology-made paddle. It became popular in a short time due to its unique pros.
If you regularly play pickleball, you must have heard of T700 carbon paddles or TORAY carbon paddles. So, what exactly is this T700 carbon? It is one of the strongest, lightest, and most durable paddle-core materials ever used. Here is a basic explanation of the carbon fiber materials:
- Carbon Fiber Grades (T300, T700, etc.):
The number in front of the letter ‘T’ denotes the amount of carbon present inside the fiber. Higher carbon presence imparts more strength to the paddle with durability and performance. - Carbon Fiber Weaves (3k, 18k, etc.):
The ‘3k’ refers to the fiber count in each bundle of pickleball paddles. Normal fiber weaves accelerate ball spinning and vertical shots. The special ‘3D 18k’ weave has carbon fibers incorporated in three equal directions, instead of just vertical. This revolutionary multi-directional weave leverages impactful spin from any serving angle. The high number of carbon fiber weaves makes the fiber bundle dense and strong
I have explained the basic method of carbon fiber weave paddles below:
- Stacking RCF sheets:
Three rectangular thin sheets of raw carbon fiber are pre-soaked with an adhesive resin. These sticky sheets are stacked on each other at an alternating 90-degree angle. - Keeping a peel ply of stacked sheets:
A peel play is kept on the stacked resin-glued sheets. It absorbs the extra sticky resin in the sheets. - Applying heat mold:
These layered sheets with a peel ply on top are placed inside a hot press mold. This hot press mold adds pressure with the required heat to create a solid unibody paddle piece. The applied pressure distributes the epoxy resin evenly in the paddle’s core and faces. The RCF sheets also get saturated during this process making the paddle more durable and strong. - Peeling off the ply:
Now, the peel-ply on the stacked RCF is peeled off carefully. But, it leaves behind a rough and textured surface on the RCF sheets. This texture causes greater spins when you hit the ball on a carbon-weaved paddle. Many players think that it is the raw carbon fiber that is causing the spin. But, in reality, the texture adds spin to the paddle face.
-
Foam Edge Method:
Hybrid paddles are called ‘Gen 1.5’ because they are formed from the conventional sandwich method and thermoforming process. The main key to focus on here is they have foam-edge technology. Here is the basic way of creating a Foam-Edged paddle:
- The raw and suitable foam material is incorporated on the edge of a pre-designed Gen 1 paddle panel blank.
- This setup is introduced to hot-press. This foam expands due to applied heat and fills up the gaps and voids in the middle honeycomb core of the pre-cut paddle material.
- The manufacturers wait till the material is set up completely. The heat supply is removed and they let the processed paddle cool down. This phase makes the paddle stronger than before and more rigid.
This is how a foam-edged Paddle is made. It spectacularly has a large sweet spot and a high moment of inertia. The plus point of these paddles is that they wobble less on off-center hits and offer better control over the fast serves.
-
Thermoforming Method:
Thermoformed paddles have amazed pickleball fans due to their revolutionary structure and better control, power, and spin. These paddles are called ‘Generational 2’ or ‘Gen 2’. The Legacy Pro was the first USAPA-approved thermoformed paddle in the history of Pickleball. It is now widely used among skilled and professional picklers. Here’s the basic method of making paddles with the thermoforming process:
- A high-quality, impact-resistant, durable, and advanced polymer like Vitrimer sheet is heated till it becomes pliable.
- This heated sheet is shaped into desired paddle forms or shapes on an engineered surface. Sometimes, pre-shaped body components are also used.
- The honeycomb core and face sheets are cut into desired shapes.
- Sometimes, the foam surrounding the core is added after the thermoforming process.
- This step gives additional mechanical support to the top and bottom face sheets and fits perfectly around the edges without any gaps.
- The honeycomb core and foam edges are covered with epoxy glue or adhesives.
- Later, the honeycomb core and foam edges are sandwiched between the top and bottom face sheets.
- This setup is introduced to a two-piece mold for applying heat and pressure. It helps to create a rigid and durable unibody paddle frame.
- This previous step accelerates the crosslinking of epoxy adhesives to stick the top and bottom face together with the middle honeycomb core.
- After a certain cooling time with the same pressure, the thermoformed paddle is removed from the processing mold. This is how they create a thermoformed paddle with accurate precision!
Creating defect-free thermoformed paddles:
Sometimes the core has carbon fiber-reinforced composite sheets. These sheet’s fibers should move during the thermoforming to create a defect-free paddle. With a high-viscosity matrix, the fibers may not move easily. They may get stretched, broken, wrinkled, or voided on applying heat and pressure. However, with a low-viscosity matrix, the fibers can move fast which can cause cracks and brittleness in the paddle.
-
Laser Cutting Method:
This is a customized way to create a paddle according to your choice of core and face material, paddle color, design, etc. You may create your DIY pickleball paddle with this method.
- A high-quality laser cuts out the two pieces similar to a paddle shape. A suitable base material like a honeycomb core sheet or wood is cut with the laser in this process.
- The handle size is measured accurately before cutting the paddle base with the laser.
- These laser-cut parts undergo thermoforming or sandwich methods to proceed with paddle manufacturing.
- Laser cutting allows the most accurate and precise shaping and design printing on paddles.
-
3D Printing Method:
Two companies named, Wilson Sporting Goods and Azul 3D partnered to create paddles with the 3-D printing method. They came across two major problems that pickleball players were facing. These problems were the paddle’s pop sound and size.
The regular paddles make excess noise after hitting the ball. This loud sound can be noisy and disturbing for the people living near the courts. Back in 1965, when this sport was discovered, the paddle sizes were as big as a ping pong racquet. The paddle’s size needed to be optimized according to the player’s needs.
Wilson Sporting Goods and Azul 3D came up with the idea of HARP technology combined with stereolithographic printing. This 3D technology transforms liquid polymer into solid objects with the help of ultraviolet light. This printing works on 5 pillars such as:
- part consolidation,
- novel geometries,
- customization,
- digital inventory, and
- localized manufacturing.
- Part Consolidation:
Using this technology, their LAKE 3D printer can print out the structure of two wooden handles, two fiberglass faces, and a middle honeycomb core to print them in one piece. It can print 156 custom-sized paddles in 24 hours which means 57,000 paddles within a year.
- Novel Geometrics- Quiet paddles:
Regular pickleball paddles contain honeycomb core and fiberglass faces. The honeycomb core is sourced from materials that are used in airplane parts. These materials are hard and it makes this paddle too noisy.
Azul 3D and Wilson developed a special material that is strong, durable, and noise-resistant. Traditionally, while manufacturing paddles, some voids or gaps may remain in the core or faces while sealing them.
The special material created using Azul’s 3d technique eliminated the traditional sealed chambers. It can cover the holes and gaps in the paddle face and core columns. It helps to reduce and change the noise frequencies at lower levels. Players can get the pop effect but there will be no itchy noise.
- Completely Customizable Paddle:
Traditionally manufactured faces are attached to the core printed with Azul 3D printer. This transparent paddle design can show the flexibility of the core. The customized core materials can withstand hard hits and bring a unique customizable look.
These 3-D printed cores can have square, triangle, hexagonal, etc., shaped lattices. It can balance the density and lower the chances of dead spots that appear in the regular paddles. Also, players can choose the color, grip size, and paddle size to increase their performance and maneuverability.
How To Build a DIY Pickleball Paddle?
I am a pickleball person who learned this game when he was a little boy! Me and my brothers and I decided to create a paddle on one Sunday afternoon. I believe he is one of the best mechanical engineers. He has all the knowledge of manufacturing required to create DIY pickleball paddle! Here’s the quick step formula to create a paddle of your own at home:
- Cut out paddle face and core:
You can select wood for faces and honeycomb polymer for the core. Cut the two wood faces and middle core of 3/ 8 size each. Use a suitable cutter like a scroll saw for accurate cutting. - Cut out the handle:
Similarly, cut the handle of 6’ from the available wood board. - Cut out the notch:
Use a small-sized cutter like a hacksaw cutter to cut out the notch. The paddle handle should slip in the notch. Use a flat file to smoothen the corners of the notch. - Assemble the parts:
Use a strong glue like wood or gorilla glue to attach the core to the faces. Slip the handle inside the notch. Use wood glue to stick both parts. Log 2 to 3 nails inside the handle and notch structure to fix them. - Add a hook:
If you want a wrist strap, add a hook at the base of the handle where the notch ends. You can add a durable string of your choice to this hook. - Coat the faces:
Make the ends smooth and scratch-free as wood is likely to feel rough. Sand the wood up to 40μm size. Coat the paddle with a suitable layer of paint and a sticker if you wish. It leverages the look of the paddle. - Layer the grip:
Take good-quality Vinyl tape and layer the grip from the bottom of the handle to the top. You can use hockey tape if the vinyl tape is unavailable. - Add an edge guard:
Add a super-glue layer to the paddle edges and stick the edge guard. Make sure you cover each area to avoid any gaps and voids. Edge guards sustain the paddle for a longer time.
And, Voila! Your DIY paddle is ready to rock on the pickleball courts!
Conclusion:
Understanding pickleball paddle-making is crucial for players. A right paddle can remarkably improve the player’s performance, playing style, and gameplay. I hope this guide on ‘how is a pickleball paddle made’ has given you meaningful insights for choosing your preference and skill level to select the ideal process. Whether it is thermoformed or an RCF, you can handle the paddle well if you apply the right tactics. From my experience of playing pickleball for years, I would suggest learning about the paddle construction methods and choosing the best suitable paddle based on your playing skill level!
Till then, see you in court.
0 Comments